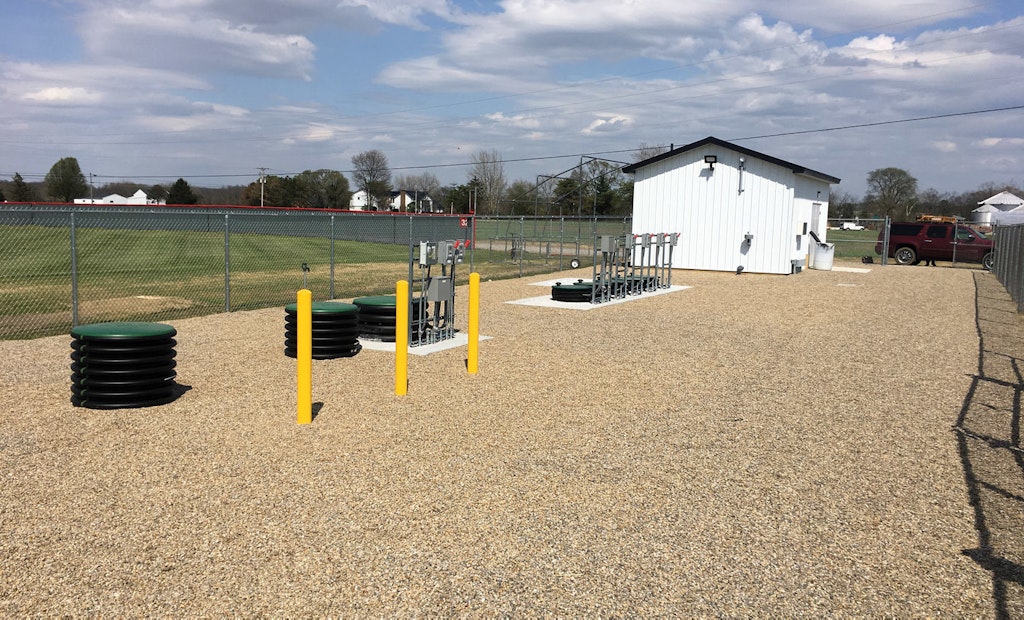
The completed sequencing batch reactor at Logan Elm School District is sandwiched between a track (unseen on the right side of the image) and a baseball field visible at left. At left center are the risers for the equalization dosing tank. In the center are the risers for the SBR tank. The white building holds a blower for the SBR and the UV system. Infiltrator Water Technologies supplied risers and lids for the SBR tank. Risers on the primary tank were HDPE pipe with BrenLin lids. Panels are from Fralo Industries. (Photos courtesy of Earthtek)
The Logan Elm School District had two schools, two package plants and too many permit violations. One plant served the junior high school, and the other was added when a high school was constructed. Now the district was in need of a new system to end the violations.
To remedy the problem, the district in Circleville, Ohio, hired engineers who looked at the options.
“We looked at traditional systems. A small package plant with traditional sand filters was what the school had,” says Jeff Baird, an engineer with the design firm of STONE Environmental Engineering & Science in Columbus. But a sequencing batch reactor was a better choice because of the highly variable flows.
When school is out of session, there is very little wastewater in the system. In a large plant, bacteria populations would not be stable under those conditions. The SBR can be adjusted, and in this design, half of it can be shut down. “That actually keeps the plant healthier,” Baird says.
The project was divided among several firms. Shaw & Holter of Lancaster was the general contractor. SBR design and equipment came from Earthtek Environmental of Batesville, Indiana, which also helped with installation.
The system
From the collections system, wastewater flows through an 8-inch Schedule 40 pipe into a 15,000-gallon primary fiberglass tank from Containment Solutions. A baffle with 6-inch round holes positioned 4 feet above the floor splits the tank into two compartments. The first compartment settles solids. In the second compartment are two Sabre 1/2 hp pumps. These feed the SBR through 2-inch Schedule 80 pipe. Submersible pressure transducers from PMC Engineering measure the water levels in the tanks.
The SBR is contained in the next tank, also a 15,000-gallon model from Containment Solutions. Wastewater is mixed with a Sabre 3 hp pump and aerated with two FPZ 4 hp regenerative blowers with one active and the second a standby. Effluent is captured by a pair of floating decanters with weirs. A 3 hp Sabre pump on each decanter inside the SBR sends effluent through a single 3-inch Schedule 80 pipe to an above-grade building. Effluent goes through a filter from Forsta Filters and then to an Amanda UV system that provides tertiary treatment. The UV system has two treatment chambers with four lamps per chamber. Each chamber can treat the entire flow in the event the other must be offline for maintenance.
Inside the UV building is also a Webtrol 5 hp pump with a variable-frequency drive. It provides additional power to push treated water to the surface discharge and also handles backwashing.
A pair of programmable logic controllers runs the treatment process. Before effluent is pumped out of the SBR, the system goes into idle for about 60 minutes to let solids settle. While that’s happening, the controllers turn on the UV lamps to warm them up. Once the decanting and tertiary treatment is complete, the controllers turn off the UV lamps. That saves the district a little bit of money and extends the life of the lamps, says Bannon Young, operations manager for Earthtek Environmental.
As water leaves the UV units, it passes through a venturi that pulls air in to oxygenate the water, and water then passes through an autosampler from Manning Environmental. Effluent discharges into a nearby creek.
A 2-inch recirculation line diverts some sludge from the SBR back to the primary tank. That is done from the second tank with a pair of 1/2 hp Sabre pumps running on a timer after effluent is decanted. The operator watches the sludge level and maintains 2 to 2 1/2 feet, Young says. Every one to two years, the primary tank will need to be pumped out. Because the sludge and primary pumps are the same kind, they can be switched out in case of failure.
“It’s not necessary to do this when we build a plant, but it’s always nice to have that extra bit of reassurance,” he says.
The system is run by a Fralo Industries panel that commands the PLCs and displays information on a touch screen. The PLCs are connected to the internet so the operator can monitor and control the plant remotely.
Infiltrator Water Technologies supplied risers and lids for the SBR tank. Risers on the primary tank were HDPE pipe with BrenLin lids.
After a lot of research and a recommendation from a fiberglass company, Earthtek Environmental developed its own technique for bonding risers to the tops of tanks. Technicians cut the rib off the HDPE pipe end. This stub is heat-treated to remove oil in the pipe, then sanded and sealed into a channel in the tank opening collar with fiberglass resin. The fiberglass makes a permanent, watertight seal between the tank and riser, Young says. The Infiltrator Water Technologies risers were sealed into the SBR openings in the same way.
Hurricane delay
The project had a schedule until Hurricane Harvey hit the middle Texas coast in the fall of 2017. That’s where the Containment Solutions tanks were being manufactured, but the storm knocked everything out of sequence.
That delay in delivery was enough to push completion of the project into the spring. So the electrical subcontractor did his work through the winter. “It took a lot longer to do the electrical work than we anticipated,” says Ed Shaw, who co-owns Shaw & Holter.
For the project, the company used a Cat 322 excavator, John Deere rubber-tired backhoe and a Cat 253D skid-steer. Tanks were set with a Lorraine MC30 30-ton crane that belongs to the company.
“We put in one dewatering point because we were a little afraid of the tank floating, but we didn’t really have a lot of rain,” Shaw says.
Once the new plant was operational, the old plant was demolished.
The project prepares the district for a new future, and on Nov. 6, 2018, voters approved one. A $44 million bond issue passed to fund construction of a new K-12 building to replace the present high school.