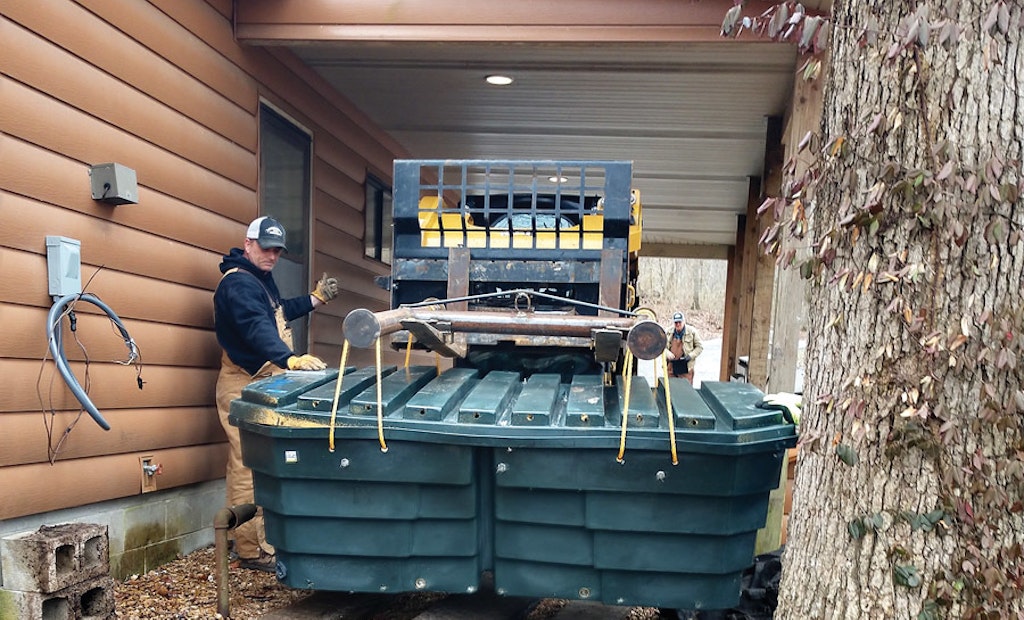
Because of the tight space and low clearance, Stewart Concrete fabricated a custom frame that the LaFollette Excavating team could use to lift and swing the Puraflo pods. Excavator Billy Lewis, left, helps guide the pod. (Photos courtesy of Jeff Julien/Stewart Concrete Products, and Larry LaFollette/LaFollette Excavating)
As the sale of a waterfront property proceeded in Rogersville, Missouri, a home inspection found the onsite system was not up to code.
“There was an existing wastewater system, but it was 40 years old. Nobody knew what size it was or where it discharged,” says Larry LaFollette. He co-owns LaFollette Excavating of Strafford, Missouri, which installed a replacement system.
The two-bedroom house was built as a recreational residence and sits on a bank about 25 feet above the James River, which made the project environmentally sensitive. The owner liked the home so much that he took up permanent residence, LaFollette says. Expected flows are 120 gallons per bedroom, so the 360 gpd capacity of the new system allows for some extra flows. That’s a fairly standard capacity for systems in the area, LaFollette says.
The team looking at the new onsite solution settled on a Puraflo system from Anua. “The other option was a holding tank and pumping it out monthly,” LaFollette says. The county wasn’t keen on that option, he adds.
New system
Because the lot is very small, the system starts at a septic tank beside the house and ends at Puraflo pods around a corner behind the house.
Wastewater leaves the house in a 4-inch pipe. It runs about 10 feet and empties into the septic tank from the old system. “We were able to able to reuse the septic tank because we were adding on a larger pump tank,” LaFollette says. The existing septic tank is a 1,000-gallon concrete model with three chambers. All are now used for settling solids.
At the outflow is an 8-inch filter from Polylok. A 10-foot run of 4-inch pipe takes water to the pump tank, an 800-gallon polyurethane model made by Infiltrator and supplied by Stewart Concrete of Halfway, Missouri. Inside is a single Zoeller pump discharging through 2-inch PVC to a pair of Puraflo modules set about 3 feet deep and with their lids at grade. A panel from SJE Rhombus controls the system. Floats control the dosing, and each dose is 120 gallons. Beneath the pods are 6 inches of 1-inch-diameter stone to accept the effluent.
Peat filters like Anua’s Puraflo have a large surface area for treatment and a large capacity to hold water, according to the University of Minnesota Water Resources Center. Unsterilized peat also brings with it a variety of microorganisms, and the result is a high-quality effluent that is especially well suited for environmentally sensitive areas.
To do the job, LaFollette’s team used a Cat 299 skid-steer and a rented IHI mini-excavator. The excavator had to be rented because the canopy on LaFollette’s own excavator isn’t removable, and the team needed lower clearance so the machine would fit under the carport at the side of the house.
They also rented a bucket on tracks to move stone to the Puraflo beds.
Lack of space
Aside from needing a special permit from the county, the team’s other challenge was the very tight space. At the rear of the house was a sliver of land between the house wall and a retaining wall and fence that kept people from falling down the riverbank.
Landscaping blocks covered the existing tank at the side of the house. Equipment had to move over this, so the LaFollette crew laid 2-by-12 planks to distribute the weight of equipment.
Because there was only one point of access, the crew started from the far end, setting the Puraflo units first and working backward, “kind of like painting yourself out of a room,” LaFollette says.
Moving the pump tank to its position was easy. Lightweight, technicians carried it by hand. Moving the Puraflo tanks to the back of the house was another story. The low carport roof restricted the height of any equipment carrying the tanks, and beyond the carport there was limited room to swing equipment. A representative from Stewart Concrete came up with a solution.
The company fabricated an H-shaped custom frame using 3-inch steel pipe with quarter-inch walls. Angle irons reinforce the corners. Polypropylene rope on the Puraflo pods slipped over the ends of the frame. The skid-steer operator could slide the fork under the frame and float the tank a few inches off the ground to move it through the carport.
“And once we got out from under the carport, we could pick it up higher and swing it around so we didn’t hit the fencing,” LaFollette says. Setting was done with the mini-excavator. The crew took down a portion of retaining wall and the fence on top of it to provide space for the mini-excavator to move.
A fully loaded pod weighs 1,500 to 1,800 pounds, LaFollette says. When the job was done, the frame stayed with Stewart. That way, he says, it’s available for other contractors to use as well.
Technicians will check the pods as part of their annual maintenance work on the system, LaFollette says, and the company’s four-page report (like the maintenance report for a car) shows the homeowner how the system is doing. When the peat shows signs of breaking down, in about 12 to 15 years, it can be easily sucked out with a vacuum truck and replaced, he says.
Teamwork on the job was very good, LaFollette says.
Michael Bowers from the Greene County Environmental Division was a great help in getting the needed special permit through the process, he says. That took a couple of months.
The previous owner also had a good attitude. She was the widow of a local builder and wanted to do the right thing, LaFollette says.
“She called us. We’d worked with her husband quite a bit,” he says. “She volunteered to pay for the whole system. She wanted to do it right and make sure the new owners were happy … and didn’t add to the price of the house.”