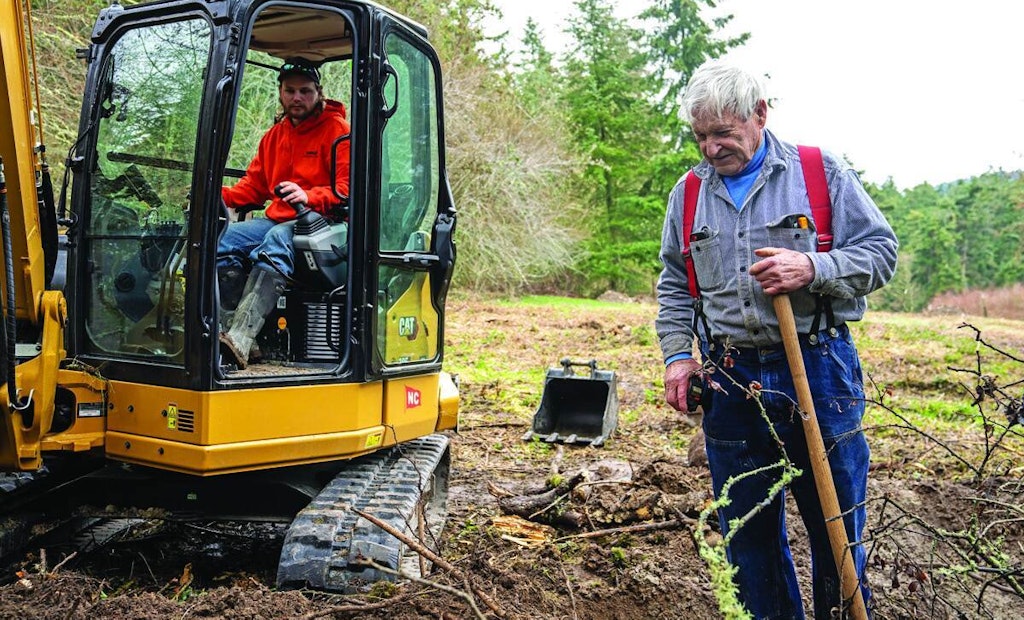
Stonebridge and Madsen, in the Caterpillar excavator, search for a lateral line while making a drainfield repair in Coupeville, Washington.
Interested in Business?
Get Business articles, news and videos right in your inbox! Sign up now.
Business + Get AlertsIn 50 years of onsite work, Jerry Stonebridge has seen many changes. Some made his work easier. Some will change the industry. And he continues to adapt his business even as he contemplates retirement.
While working at the University of Washington School of Rehabilitation Medicine in 1972, Stonebridge began working in the onsite industry. In 1976 he launched Stonebridge Construction Company on Whidbey Island, Washington. As the company’s work included more onsite jobs, he changed the company name to Stonebridge Environmental.
Whidbey Island sits at the top of Puget Sound, opposite the northern suburbs of Seattle. Between 2010 and 2021, the population of Island County, of which Whidbey Island is the major part, grew 11.4% to just over 87,000 people.
Like other places near booming cities (the population of Seattle increased 21% from 2010 to 2021), Whidbey Island has high housing prices. “I just got a notice from a real estate person,” Stonebridge says. “On the south end of Whidbey Island, the average residential sale was $700,000.”
Most of the island’s shoreline used to be lined with fishing cabins, Stonebridge says. “So what is happening now is, people are buying these fishing cabins and turning them into million-dollar houses.” Then the question is how to fit a large house and a wastewater system onto a relatively small lot, he says. For people with enough money, onsite options along the shore can be broader. Some people buy another lot, perhaps upslope, and then install an offsite drainfield, he says.
ADVANCED TREATMENT
One of the changes he’s seen during his career is having technologies to deal with tight lots and high water tables.
Initially he used sand filters for shoreline lots and mound systems on larger parcels with shallow soils. As large houses replaced cabins on the shoreline, he says, the space for onsite systems shrank, which required a variety of advanced treatment units.
“When we do repairs on the shoreline, we can’t get a truck and crane to the site, so we have to be able to put the aerobic treatment units into tanks that aren’t concrete,” he says. “A lot of times you have a house, and you’re working on the beach right in front of the house, behind the bulkhead. Lifting those concrete tanks over the house is a little bit dangerous.”
Use of advanced technologies is also required by regulations. “We have very, very strict regulations on what we can do on our shorelines. Almost anything we do is secondary and tertiary treatment,” he says.
Away from the shoreline, the equipment he installs includes some gravity and pressure-distribution systems, drip distribution and mound systems.
Soils differ throughout the island, which was covered a couple of times by glaciers, Stonebridge says. He takes soil logs for every site and designs according to those. Plus, he adds, the state requires 3 feet of vertical separation between the bottom of a trench and the impervious layer or water table. “If you can’t maintain that, you have to use an ATU with pressure distribution or an above-grade system such as a mound or an OSCAR (onsite sand coil area recharge).”
BUSINESS STRUCTURE
Installations are about 60% of his business, Stonebridge says. Design and inspections account for another 20% each. “We can do as many inspections as we want. It’s very busy on that side of the business.”
The Island County Health Department requires onsite system inspections when a property is sold, requires annual inspections for aerobic treatment units and anything with a pump, and inspections every three years for gravity systems, he says.
“The inspector determines if it’s necessary to pump,” he says, “because the thing you have to remember, on Whidbey Island, there are a lot of second homes, so they don’t have to be pumped as often.”
Stonebridge estimates he does one to two designs a month. That business is so busy, he adds, that he’s never stopped to count his output. “With all of the tools that we have for designs now, you can go through them pretty quickly.” He also makes site visits to look at soils, take measurements, and gather other information he needs.
“There’s not a lot of commercial on the island. I inspect almost all the commercial systems on the south end of Whidbey Island. We’re doing some repair designs now for some commercial centers that are growing, and they have to expand the onsite systems,” he says.
His company also does O&M work, Stonebridge says. Stonebridge Environmental used to pump tanks, but now he refers that work to another company on the island.
As for marketing, there isn’t any. “I am so busy, I quit advertising years ago. The island is one of those places where, if you’re good or bad, it spreads all over the place,” he said. “It’s about customer service, taking care of the people.”
INDUSTRY CHANGES
“I think the major thing that has changed is technologies that are now available to all designers and engineers in the laser, GPS category.” Using a GPS receiver, you can specify a control point and make very accurate measurements to create a design or to guide an installation, he says. “Just Google Earth gives you the ability to look at a site even before you go out there.”
Control panels are so much more versatile now as well, he says. “So you can control different zones where you want to put effluent, and the quantity of effluent that you can put out into those different zones.”
That is not to minimize treatment technologies: aerobic treatment, bioreactors and drip dispersal, he says.
Another positive change, he says, is simply people talking to each other. Pumpers and installers are all talking to each other, he says, and training is online and widely available.
“You know, when you go to these conferences, you learn just as much in the hallway as you do when you’re sitting at the desk listening to speakers, because that’s where you’re exchanging information with different people who have a little bit different experience than you might have,” he says.
“Now we’re talking about health safety and pathogens. When we started nobody paid any attention to that. We just went to work,” he says.
“I think the other side of that is that regulations and regulators have changed. They’re now working with us to get the regulations up to the technologies that we have,” he says.
YOUNG TALENT NEEDED
Technology and reporting on system performance have changed for the better since Stonebridge served as president of the National Onsite Wastewater Recycling Association from 2007 to 2009.
“When I was president of NOWRA, one of the things we were always hammered on in Washington, D.C., was, ‘How do you know these systems are even working? Where’s the data that says these actually work on the sites?’ And we didn’t have it at that time.” With responsible management entities and county requirements for regular reports, much of that data is now being collected, he says.
With risers and inspection ports on the surface of the ground, operations and maintenance have become very easy, he says. “We really didn’t have an O&M industry. Now, in our state, we have a huge O&M service provider industry.” In Washington that’s probably the part of the onsite industry with the most growth, he says.
“I think one of the areas where we suffer most in our state is a shortage of designers because it’s a difficult test and requires four years of experience. You can get credit for college if you’ve gone to college and took courses that would relate to design work,” he says. There is also need for more installers and O&M professionals, he says.
These needs for people spring from the smaller labor force, he says, and there’s a parallel need to encourage young people to think about the skilled trades as a career. For example, he says, Washington requires a licensed electrician to install pumps, control panels and components that use electricity, but electricians are so busy they’re not interested in the work.
Among his licenses is an electrician’s license. Stonebridge says he uses it regularly because of that shortage of skilled tradespeople. “We’ve got a system in the ground, the homeowners got occupancy, and we can’t get an electrician to wire, so I’ll just go do it,” he says.
He’s found a local electrician who knows how to wire the systems Stonebridge Environmental installs, and Stonebridge says he’s trying to shift as much work as possible to that local guy.
For the future, he sees the onsite industry moving heavily into reuse technology. That means not only reuse of wastewater but drinking water and stormwater. “If you don’t have water, you can’t live. They think there’s immigration now. When a lot of these areas totally dry up, people are going to move,” Stonebridge says.
Even on Whidbey Island, he says, people who owned lots years ago drilled wells about 50 feet from the sound, and now saltwater is infiltrating them.
Treating contaminants, such as the PFAS chemical compounds that are in the news lately, will be another area for growth, he says.
TRANSITION
A couple of 305.5 Caterpillar mini-excavators, a couple of 239 Cat skid-steers, and several dump trucks comprise the equipment selection of Stonebridge Environmental.
Working with Stonebridge are Suzi Stonebridge (his wife), Bill Schild and Logan Madsen. Schild helps in the office and works with Stonebridge on O&M jobs. Madsen does installations. It’s Madsen whom Stonebridge is training to take over that part of the business.
Neither of his two sons were interested in the business, he says. Jeff is a general housing contractor, and Ted operates a municipal water plant near Seattle.
“I didn’t do a good job with succession planning. All people who start a business should have a plan of how to get out of the business,” Stonebridge says. He should have started thinking about succession when he started the business, he adds.
Madsen’s father and uncle run a heavy equipment company, and Stonebridge says he approached them about bringing Madsen into the business. Madsen is 24, has worked in construction since he was in high school, and can operate all types of equipment, Stonebridge says. In 2021, Madsen qualified for his installer’s license. He is also an island native, Stonebridge adds, “and I’ve known his dad and his uncle since they were little kids.”
Impetus for a transition came from his wife, Stonebridge says, who is ready to retire and wanted him to be free also. He thought about walking away from the company, but he said he’s particular about his customers. “I felt if I can train somebody to think the way I do, and do things the way I do, then people will be satisfied. So it was more about taking care of the customers,” he says.
He started Madsen’s training by taking him along on jobs, and he essentially became an apprentice, Stonebridge says. “Even if I retire, I’ll help him,” Stonebridge says.
KEEPS WORKING
Stonebridge turns 82 this month. He recently renewed all of his licenses for a couple of years. Now, he says, he’ll see how much use he makes of them. “I would stay on the design side to keep the installation business moving forward,” he says.
He may cut back on business, but he’ll never leave the island. Travels have taken him around the United States and the world, he says, but he’s seen no place as pretty as Whidbey Island.
Stonebridge’s 50 years of quality work in the onsite field played a role in protecting the environment and preserving the island’s beauty.